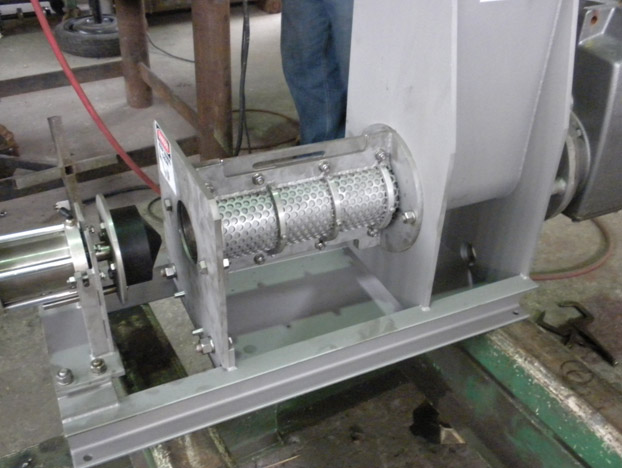
Between 2008 and 2010 Vincent ran tests involving guayule for two firms. Neither project went ahead, and at this point the NDA’s have expired.
Guayule is a 2’x2′ plant that can be grown, with little water, in the Southwest and Australia.
The technology had roots in an Arizona factory which Firestone built on an Indian reservation in the late 1980’s. That facility is now long gone. The idea was to extract latex from the guayule plant to make natural rubber.
Our original testing was done with material which was simply ground guayule plant mixed in water. The as-received was 9% solids; we got 50% solids in the press cake and 4% solids in the press liquor. Those were encouraging results.
A year later more sample material was sent to Tampa. This may not have been representative. It apparently was made from some guayule 3/8" pellets, presumably with the latex removed. These were reconstituted with latex and solvents (hexane and acetone). That is what we pressed.
The press cake from testing this sample came out an incredible 82% solids! The press liquor was 11% solids. This was achieved with a light cone pressure.
We started at 10 rpm and the screen blinded. Of all things, cranking the speed up to 70 rpm got us a strong flow of press liquor which seemed to continue without blinding.
We tripped out on high amps. However, this was most likely because the latex formed rubber cement which got between the cone and the shaft of the screw.
We were using a wedgewire screen with slots that were 0.015" wide. That worked fine. There was no sign of material plugging elsewhere in the press.
Our third round of testing was conducted in a rubber laboratory. In the research center a 5-gallon charge from a reactor vessel was fed to a Vincent CP-4 screw press. This material was guayule latex dissolved in acetone and hexane. The material was 18% solids, but this was deceiving; it looked like the insoluble solids (woody fiber) were much lower.
It was the press liquor, containing the latex, which they were trying to produce.
The press cake also had some latex left in it. This was not a problem because it was easy to wash the press cake with solvent and recover its latex.
The main problem they had was excessive insoluble solids in the press liquor. These ranged from 7% to 16%. (That must have been a percentage of the final latex, not a percentage by weight of the press liquor.) These solids were "sawdust & dirt". It looked like fine dust mixed with very fine woody fiber. We had expected the dust to go through the screen, but we could not explain why the woody fiber also came through. They started with a screen with 0.017" slots and went to a 0.011". This change reduced the amount of fines in the press liquor.
The CP-4 laboratory press in the testing was highly modified. Instead of the normal 1-1/2 hp motor, it had a 7.5 hp motor. This allowed the screw to be run at 150 rpm.
Another very unusual feature was incorporated so that the cone was made bullet shaped and mounted off a pedestal at the end of the press. This eliminated cone bushings which had gummed to the screw shaft a year before. This arrangement for mounting the cone allowed us to end the screw short, at the end of the flights. That is, the screw was supported only by the gearbox, in a cantilever form. A similar press is seen in the photo, with a black UHMW cone.
The operation of the press was highly unusual. When they blew a couple gallons from their reactor into the press, the press sat there and churned for fifteen minutes. During that period there was a minimal flow of press liquor through the screen. We concluded it was a blinded screen and the situation was hopeless. But, quite suddenly, after fifteen minutes, the press liquor started coming through the screen, and soon there was a flow of press cake. We wonder if some chemical change was going on before the press would start working.
The press cake did seem to come out in surges, like a typical (oversized) knots press. That is, the press went through cycles of packing itself full before it would push the solids from the screened area.
As with our previous testing, the press cake was extremely dry. However, there was no indication of any jamming.
As soon as the solvent evaporated, there was rubber cement left. This cement dried just like ordinary rubber cement, all over everything. Still, when we took the press apart after we had run a 5 gallon batch from their reactor, we saw that the screw had cleaned itself extremely well.
The test data said that the solvent in the press cake had ranged from 30% to 48%, with cone pressures of only 5, 10, and 15 psi. The percentage of rubber in the press liquor ran from 4% to 6%.