February 24, 2023
Vincent Corporation was approached to help with the operational challenge of running a system with two screw presses. The presses were mounted in parallel, with the second press acting in an over-flow capacity for the primary unit. In this installation there are unpredictable requirements for intermittent up to constant need to divert flow from first press. Traditionally this involved the full-time attention of an operator to monitor the level of the inlet hopper in the first press and, when required, to manually open a valve to allow for an adjusted flow to reach the second screw press.
Our automation engineers delivered a system that handled the requirement while providing added benefits of automated routines for start-up, shut-down and CIP. This system now communicates directly with plant information systems providing real-time operational data as well as historical trend-data analysis.
At the core of the control panel is the Siemens S7 1200 Programmable Logic Controls platform. A large touchscreen (Fig. 1) was mounted on the front of the panel giving operators a graphical representation of the equipment to include motor speeds, pump speeds, feedstock flow rates, cone pressure, valve sensors as well as level sensors inside the feed-hopper.
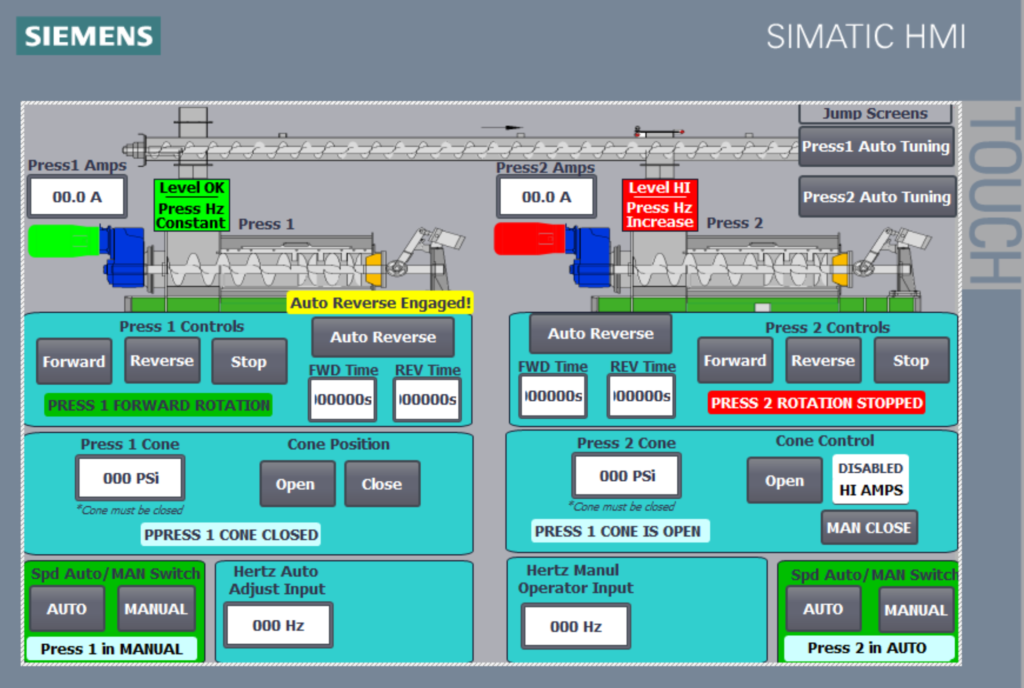
Vincent Corporation also provided an app for mobile phone, tablet, laptop or PC remote access when away from the physical control panel. All functions and operator controls are accessible via this remote access function.
A single circuit control panel linking back to the main circuit breaker houses two cabinets, one for low voltage (24 & 120v) and the other high voltage (480v). For safety, manual disconnect switches were located on the outside of the cabinet. This allows the operators to immediately and safely shutdown power to one or both of the screw press motors when required without high voltage exposure.
A UPS battery (Fig. 2), as a backup to the main power supply, was installed to allow for continued PLC communications with the plant in the instance of power interruption.
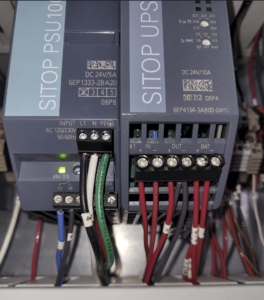
The PLC included auto-reverse functionality to prevent or clear feed stock jamming within the screw press. This is achieved through cone pressure sensors and motor amperage sensors.
Radar sensors were used for feed hopper level control. These sensors were selected based on practical experience gained in recent years. We have found radar sensors to be the most effective in applications where high steam content, random debris and other intermittent variables lead to noisy readings.
A PROFINET ethernet communication system was incorporated to provide a reliable and seamless link to the plant PLC for real-time as well as trend data analytics.
A video tour of this system can be found at https://youtu.be/AN7JIdM9hOA.
Automation Engineering Services: PLC and HMI Panel Design, Construction and Implementation
Vincent Corporation continues the drive to provide our global customer base with the latest and best technology available when it comes to helping achieve process engineering needs.
Our team of industrial design and automation engineers work directly with customers to consult and supply programmable logic controls and easy to use HMI interfaces for screw press, Fiber Filter, shredder, bulk/material handling, filtration, and distillation process engineering requirements.
The automation systems we deliver protect against operator error with start-up and shutdown routines as well as integrated failsafes. These alert operators to condition changes as well as overriding operation of equipment when required. Our automation integrates with process engineering functions. This ensures that any automated changes to the operating state or equipment are effectively communicated to any interdependent processes and any necessary adjustments are made.
Product flow control, temperature monitoring/control, washing/dosing/spray manifold functionality, cone pressure, level sensors and load cell monitoring are just a few of the initial levels of visibility, process control and trend data we can deliver to your operation.
We have extensive practical experience working with customers across the globe on single screw press requirements, multiple screw press counter-current wash systems, skids incorporating bulk/material handling, particulate separation and filtration, evaporation and distillation requirements all the way up to full facility turn-key systems.
Our in-house programmers work with Unitronics, Siemens and Allen Bradley platforms and are equally comfortable with new control panel builds as well as making changes to your existing system and programming due to process changes you want to implement. You own the code on the systems we provide, giving you full control over future changes either through Vincent Corporation or any service provider of your choice.
Our automation products come with web services functionality for remote monitoring and control of operating conditions. With this feature our engineers can remotely access your automation via a secure portal to make changes to operating parameters on your request.
ISSUE #347